R&D
Electric Vehicle Technologies Department
The Vehicle Control Systems, Hardware Design Group, Electrical Machinery Group, Power Electronics Group and Mechanical Design and Analysis Group of TÜBİTAK RUTE Electric Vehicle Technologies Department carry out important studies in various fields in the rail transportation sector. The Vehicle Control Systems Group focuses on Train Control and Management Systems, developing a comprehensive set of systems that integrate the electronic systems of rail vehicles. The Hardware Design Group responds to electronic hardware needs with high-tech and reliable systems, while the Electrical Machinery Group designs drive motors and electric vehicle traction systems for various rail vehicle platforms. The Power Electronics Group designs traction systems and auxiliary power units for rail vehicle platforms and carries out prototype production and testing. The Mechanical Design and Analysis Group, on the other hand, continues its work by targeting high safety and performance standards with detailed processes ranging from vehicle body design to crash analysis. The groups share their knowledge and experience by working in interaction on projects for the sector.
- Objective
- Working Areas
- To develop expandable, flexible, cost-effective, local resources that meet the needs of our stakeholders and are compatible with international standards.
- Central (Vehicle) Control Unit
- Control/control scenario design and applications
- Human Machine Interfaces (HMI)
- Train Communication Network (TCN - IEC61375)
- Ground central station communications with GSM
- Event Recorders and Maintenance & Analysis Software
- Rail vehicle simulation software
- Development of asynchronous railway traction motor
- Drive motor development for electric vehicles
- Development of hydrogen generators for power plants
- Development of traction converter
- Development of auxiliary power unit
- Design and optimization of power electronics systems
- Development and simulation of traction control algorithms
- Development of traction control software
- Development and simulation of auxiliary power unit control algorithms
- Development of auxiliary power unit software
- Traction Control Unit (TCU) Hardware Design, Development and Testing
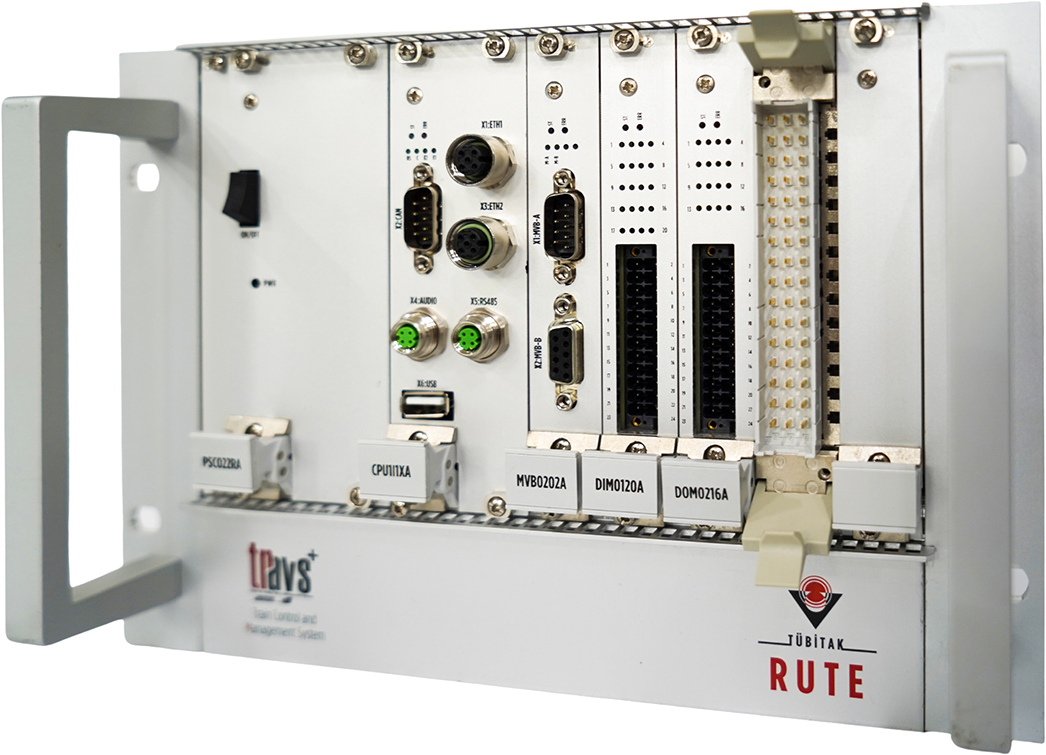
Traction Control Unit (CKU)
The Traction Control Unit (TCU), developed in accordance with EN50121 and EN50155 standards, performs traction system control, protection, recording and communication functions with electronic cards running FPGA, DSP and MCU software.
- Fiber Optic Input Output Control
- PWM Generation and Control
- Traction Control and Protection
- Analog and Digital Interface Signals Control
- Communication and Registration Unit
- Strength / Spine
The electronic design, production and testing of the modules are carried out within the Hardware Group.
- Train Control Management System (TCMS) Hardware Design, Development and Testing
RIOM - Remote Signal Input Output Module and VCU - Vehicle Control Unit
Developed in accordance with EN50121 and EN50155 standards, RIOM - Remote Signal Input Output Module and VCU - Vehicle Control Unit are electronic hardware where centralized control is realized with advanced technology software for all train subsystems.
- Central Control Module
- Analog Input Output Module
- Digital Input Output Module
- Communication and Registration Unit
- Strength / Spine
The electronic design, production and testing of the modules are carried out within the Hardware Group.
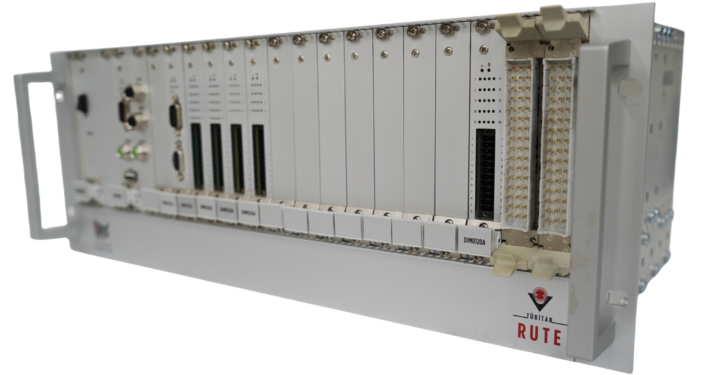
Embedded Software Development
Embedded software executed in the programmable units of our hardware is developed according to internationally accepted software life cycles. In addition to the generation of software requirements, the implementation of requirements, the integration and testing of outputs, the development of algorithms suitable for the test scenarios of the relevant hardware, version control, quality control and the production of documents of the relevant software are carried out. In this context, activities are carried out in the following areas:
Bare-Metal Software Applications:
- ARM Cortex-M based microcontroller (MCU) software,
- Serial communication interfaces, appropriate software protocols (CAN, SPI, I2C, RS-485...),
- Wireless communication protocols (GSM/GSMR, GPS, Wi-Fi),
- Real-time operating system (FreeRTOS),
- 3rd party libraries (lwip, ff ...).
Embedded Linux Applications:
- Appropriate configuration of the Yocto Linux distribution to the relevant hardware modules (System on Module, SoM),
- Module hardware interfaces and related Linux driver libraries,
- Interprocess communications (Interprocess Communication, Shared Memory).
Embedded software, together with the external interfaces of the hardware, simultaneously performs communication between sub-modules, data logging, monitoring of safety signals and many hardware control tasks through a real-time operating system (FreeRTOS).
Vehicle Body Design
Taking into account the International Specification for Interoperability (TSI) and the requirements set by customer organizations, the following activities are carried out for the vehicle body:
- Dimensioning
- Preliminary Analysis
- Concept Design
- Detail Design
- Preparation of Manufacturing Files
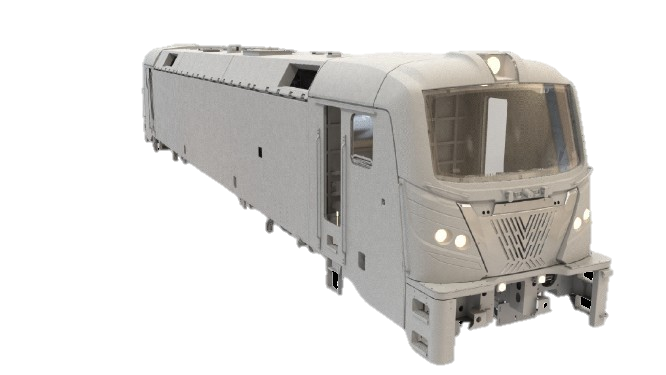
Vehicle Body Static Analysis
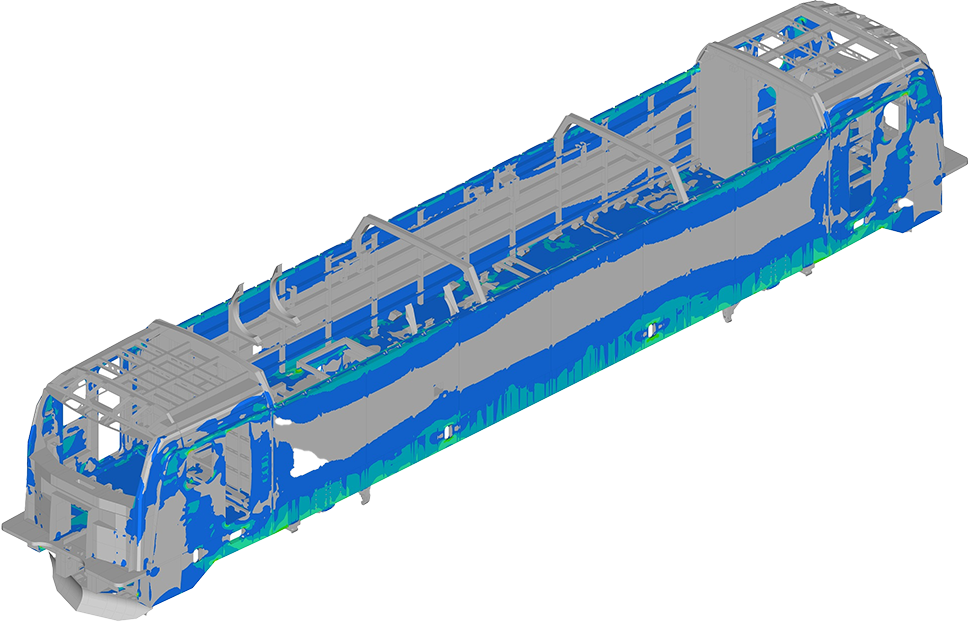
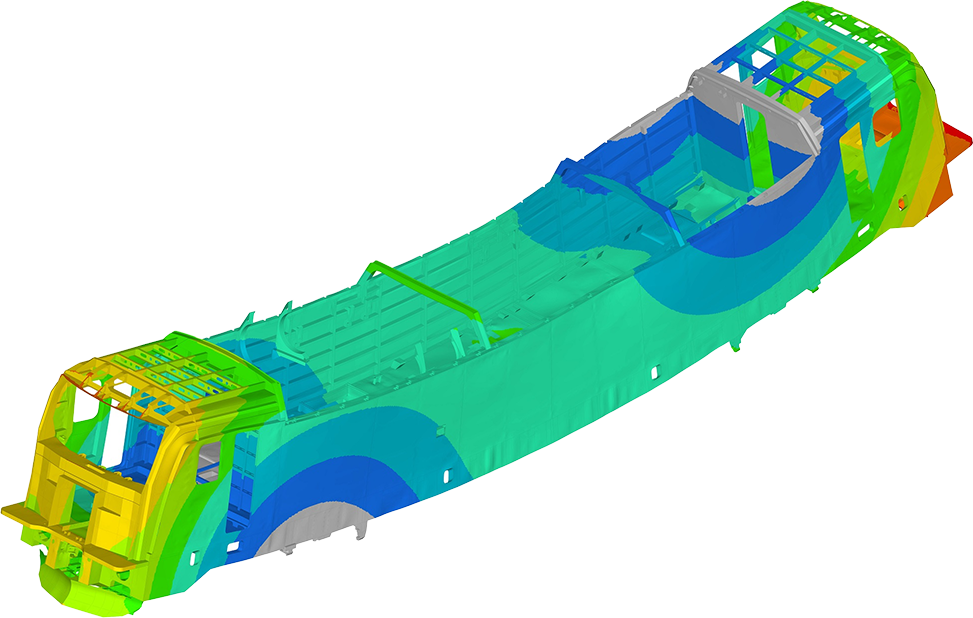
Vehicle Body Crash Analysis
Taking into account the International Specification for Interoperability (TSI) and the requirements set by customer organizations (EN 15227), crash simulations are carried out for the vehicle body under different scenarios and it is checked whether the designed vehicles provide sufficient vital volume for the machinist and other users during these simulations.
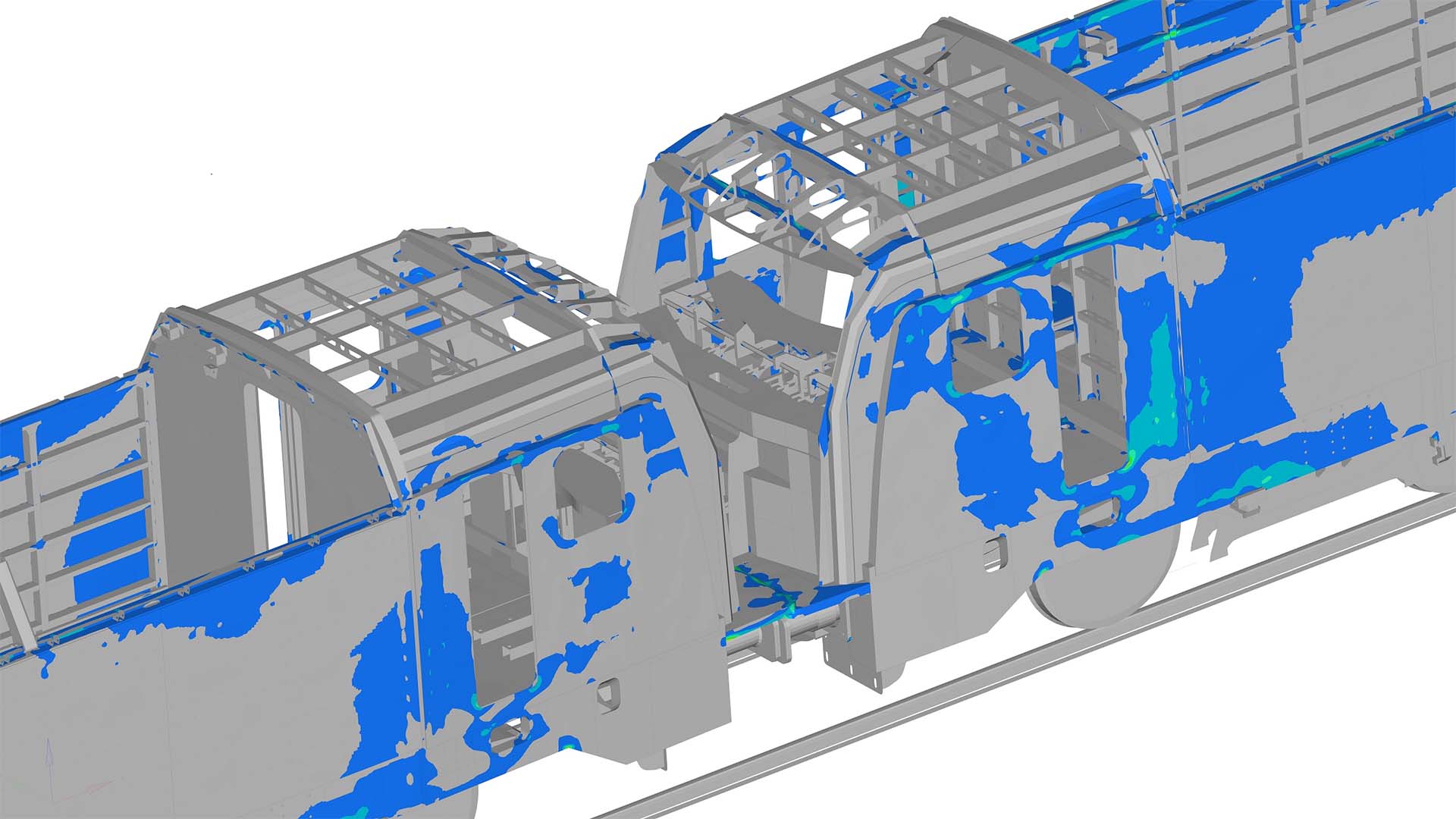
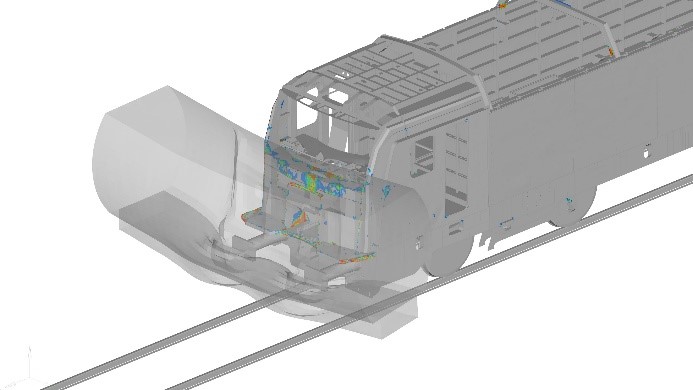
Bogie Design
- Dimensioning
- Preliminary Analysis
- Concept Design
- Detail Design
- Preparation of Manufacturing Files
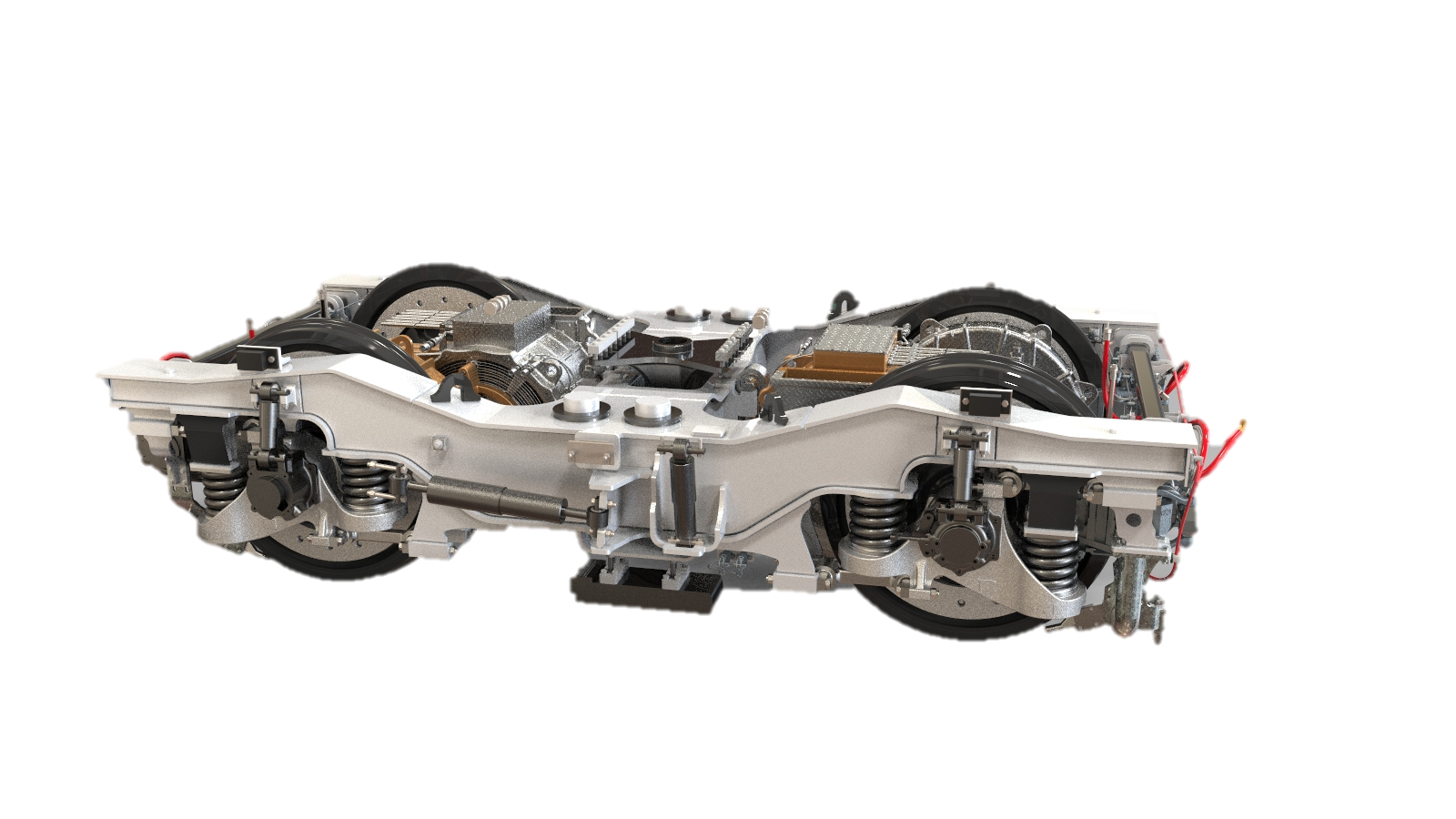
Bogie Static Analysis
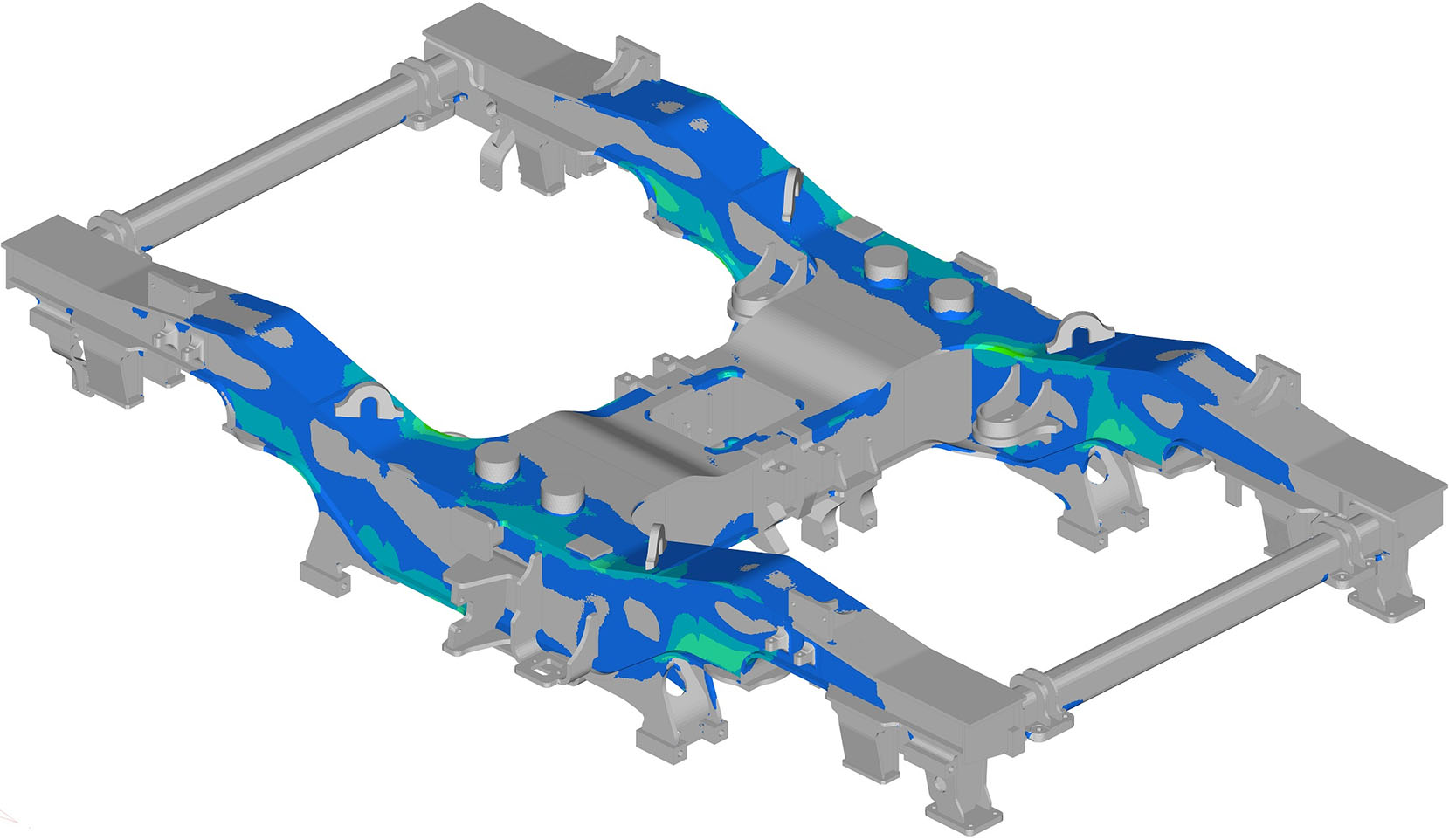
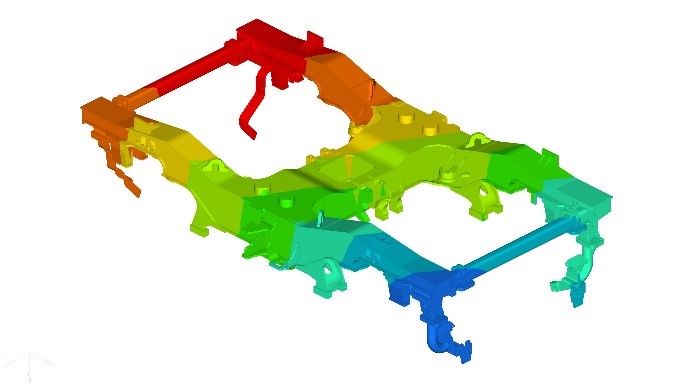
Bogie Fatigue Analysis
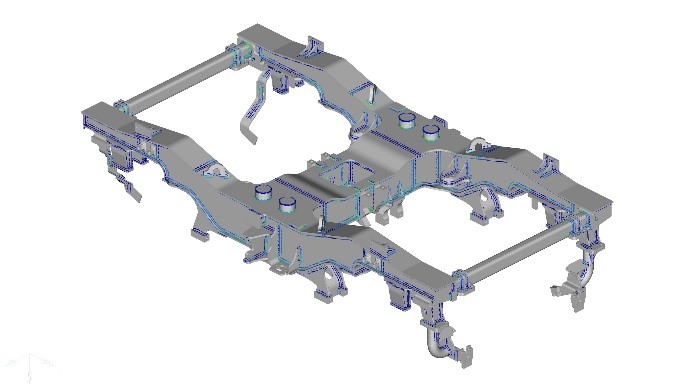
Gabarit Analyses and Kinematic Analyses
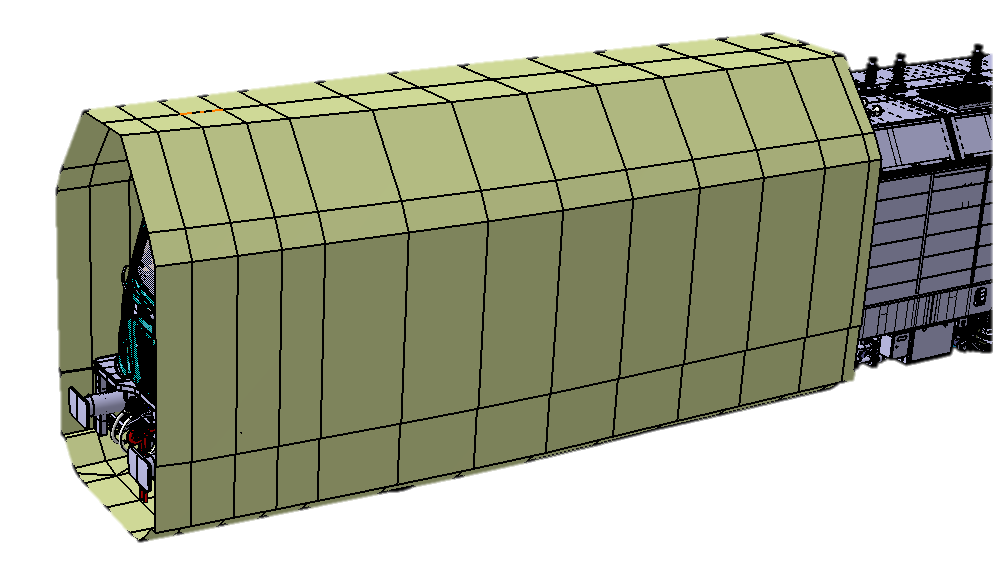
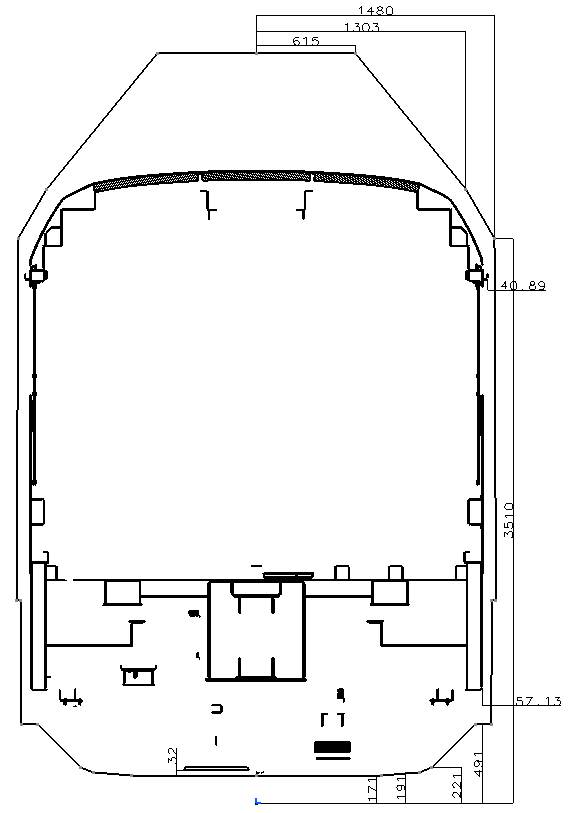
Vehicle Dynamics Analysis
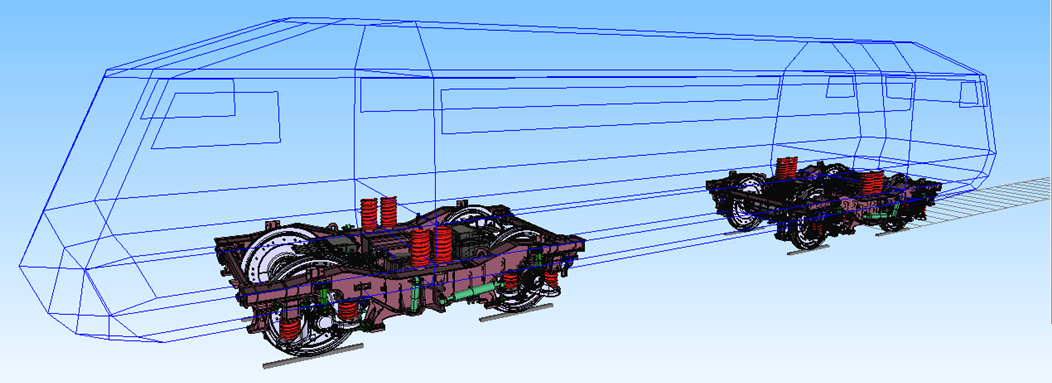
Mechanical Design and Analysis
Within the scope of Mechanical Design and Analysis, the following activities are carried out for the projects carried out within the Institute:
- Mechanical Design
- Control-free Mechanism Design
- Electrical and Control Cabinet Mechanical Design
- Cooling System Design and Sizing
- Preparation of Manufacturing Files
- Strength and Life Analysis
- Vibration, Shock and Natural Frequency Analysis (EN 61373)
- Dynamic Analysis (Explicit)
- Multiple System Dynamics Analysis
- Fluid Dynamics Analysis
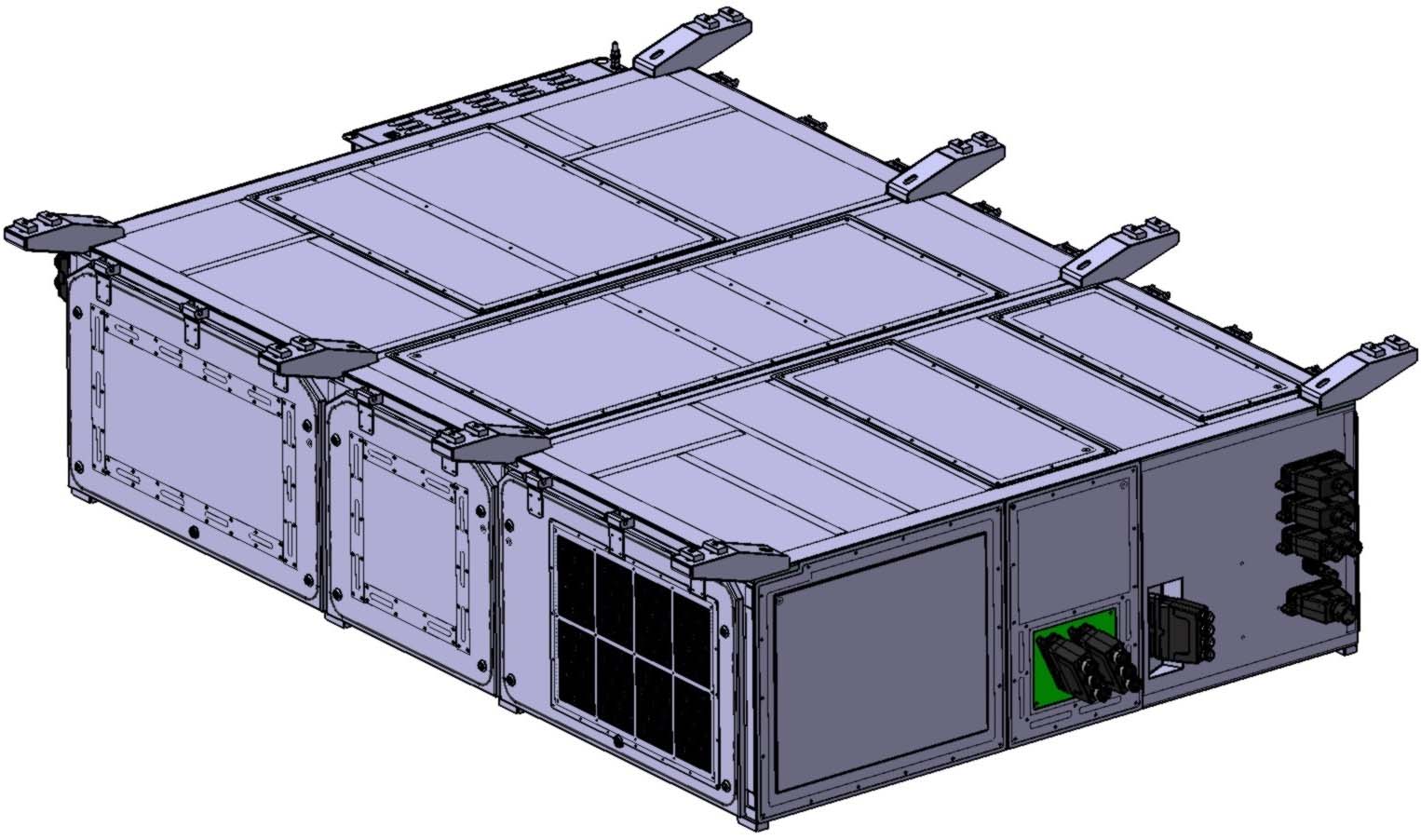
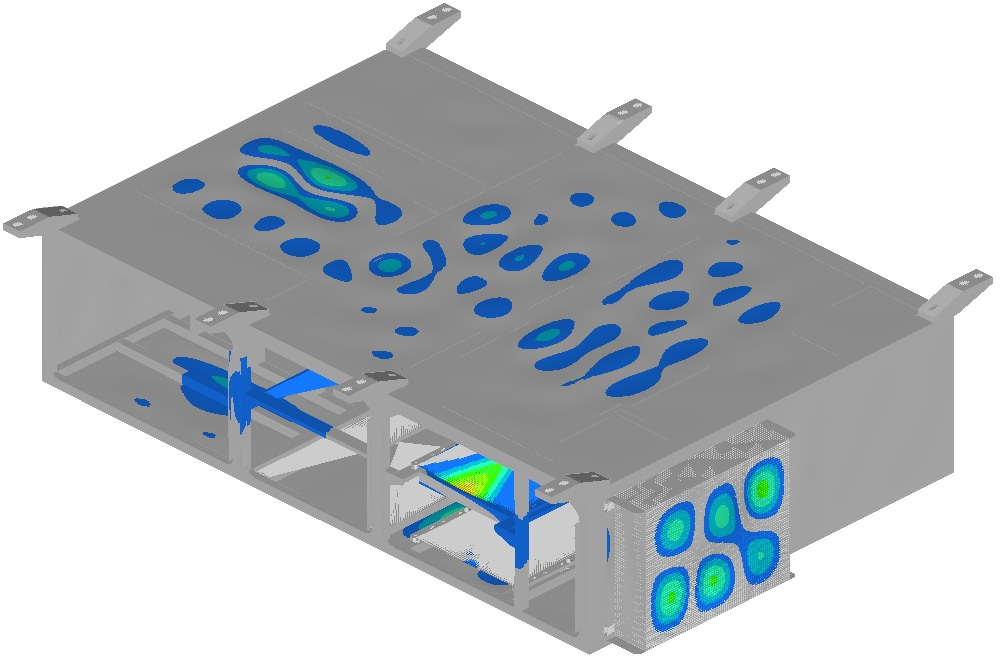
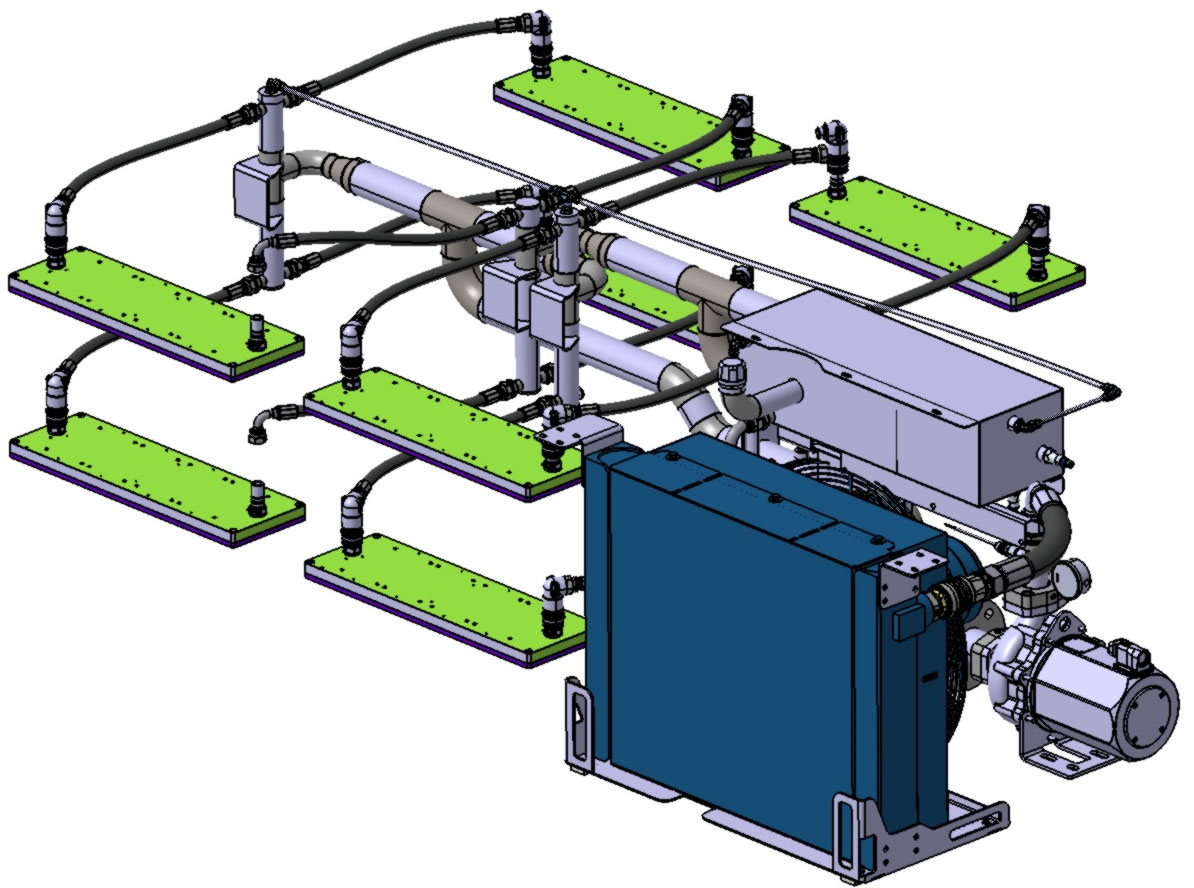
R&D
Infrastructure / Technical Specifications
- Power Electronics Laboratory
- Power Electronics HIL (Hardware in-the-loop) Test Environment
- 4-channel, fiber optic standalone door drive adapter
- 30kW, 90 l/min capacity water cooling station
- 50kW, 4,000VDC power supply
- 4-channel, 1MHz, Oscilloscope
- 6kV differential voltage probes
- 6kA current probes
- 400VAC/1.350VAC Transformer
- Licensed power electronics simulation program
- Licensed PCB design program
- Various DSP, Microcontroller and FPGA development kits, programmers and debuggers
R&D
Projects / Products
- TRAYS - TÜBİTAK Rail Vehicle Management System (E1000, E5000, Gaziray National Suburban Train and National High Speed Train)
- Development of Traction System for Diesel Electric Locomotives
- Development of E5000 Type Electric Locomotive
- Traction Control Unit for Diesel Electric Locomotives - TRACS-KP-D
- Development of Traction System and TKYS for New Generation Electric Train Sets - YEMU
- Development of Traction System and TKYS for HTS EMU 225
- Development of a New Generation Control and Propulsion System for Locomotives
- Development of propulsion motors for light rail vehicles-tramways
- Design and production of 149 kW traction motor for BURSARAY DEUWAG sets
- Development of traction motors for shunting locomotives
- E1000 Electric locomotive 250kW traction motor development
- Development of traction motors for main line locomotives
- E5000 Electric Locomotive 1280 kW traction motor design and production
- Development of traction motor for suburban trains
- Gaziray National Commuter Train 280 kW traction motor design and production
- Development of traction motor for high speed trains
- Design and production of 380 kW traction motor for National High Speed Train
- Development of generators for hydroelectric power plants
- Development of 11MVA dislocated pole synchronous generator for MİLHES project
- Development of generators for wind power plants
- Development of 500 kW dual-feed asynchronous generator for MİLRES project
- Drive motor development for electric vehicles
- Development of 30 kW liquid cooled brushless surface magnet synchronous motor
- Drive motor development for electric vehicles
- Development of 60 kW liquid cooled brushless embedded magnet synchronous motor
- E5000 Electric Locomotive Traction Converter
- DE11000 Diesel Locomotive Traction Converter and Auxiliary Power Unit
- Gaziray Milli Suburban Train Traction Converter
- National High Speed Train Traction Converter and Auxiliary Power Unit